When it comes to life on the water, one of the most crucial aspects is ensuring a reliable power source for all your onboard needs. Whether you’re out for a weekend adventure or a long-term voyage, having a robust charging system is paramount. That’s why I embarked on a journey to enhance my boat’s electrical setup by installing a Balmar XT-250 Alternator. My goal? To harness its potential and charge a LiFePo 11KWh battery bank efficiently.
Unveiling Challenges with the Balmar XT-250 Alternator
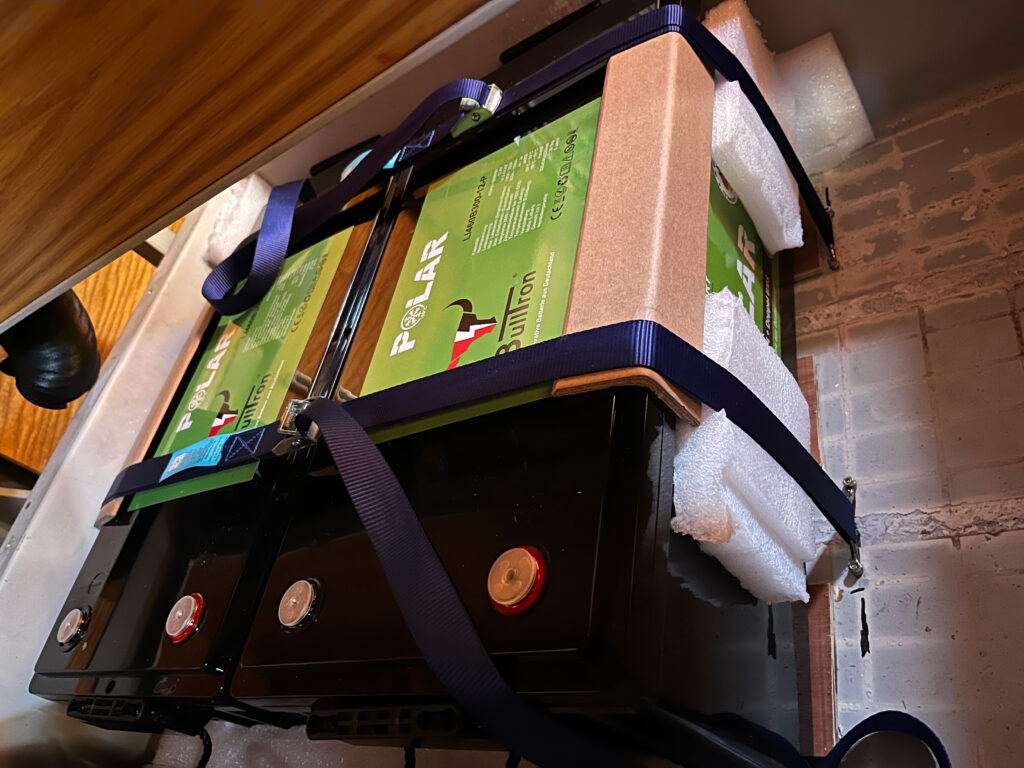
The Balmar XT-250 Alternator, renowned for its reliability and performance, piqued my interest. To make the most of it, I employed a wakespeed regulator to regulate the charging process. With a battery bank capable of accepting up to 300A, the possibilities were exciting. However, I soon discovered that pushing the alternator to its limits came with a significant challenge – excessive heat.
When there is no rush we regulate the charging to 180-200A for the wellbeing of the batteries. With this calibration we noticed that the batteries receive a maximum current charge for some minutes. However, at this point, the alternator’s temperature climbs to 100°C at the measurement point and a 115°C within the stator, triggering a derating or regulation of its output. It’s important to note that this regulation temperature aligns with the manufacturer’s recommendations.
Cooling Strategies Took an Unexpected Turn
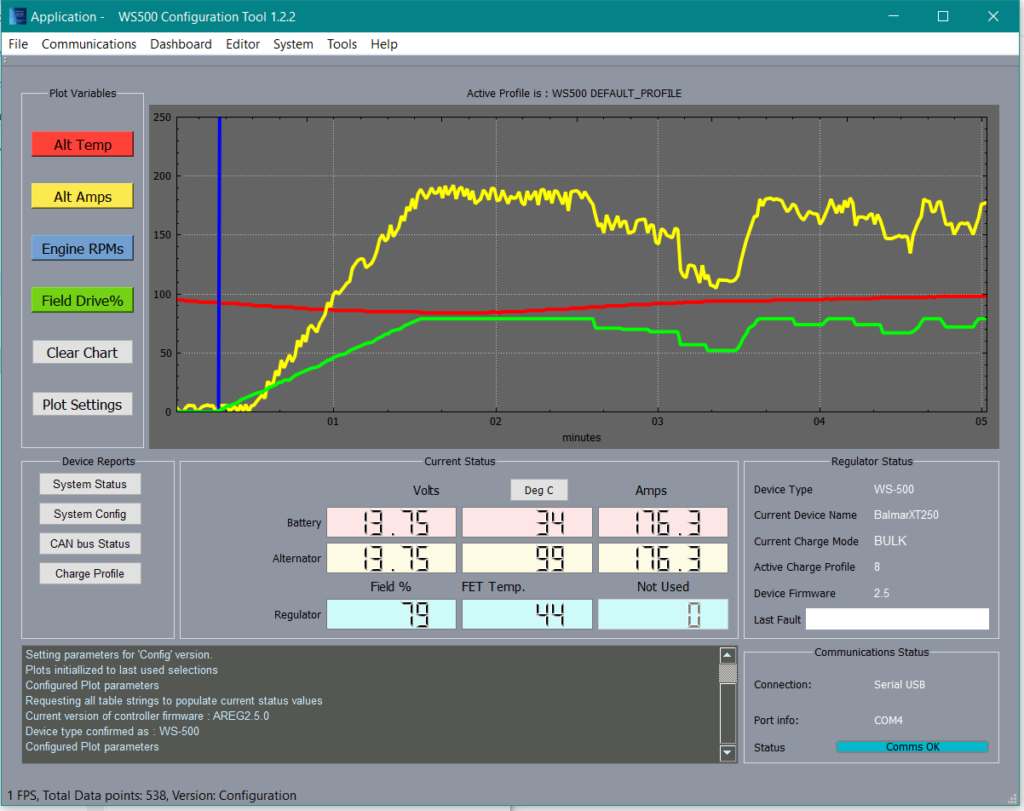
The primary concern with high-current charging became evident – the cumulative heat buildup in the engine room and the resultant alternator overheating. The regulator played its part by reducing power to keep the alternator temperature in check, but this also meant a reduction in charging current.
My first attempt involved installing a fan to expel hot air from the engine room through a pipe. Regrettably, this approach proved unsuccessful, as a peculiar pumping wave effect caused the hot air to circulate back towards the alternator. It was back to the drawing board.
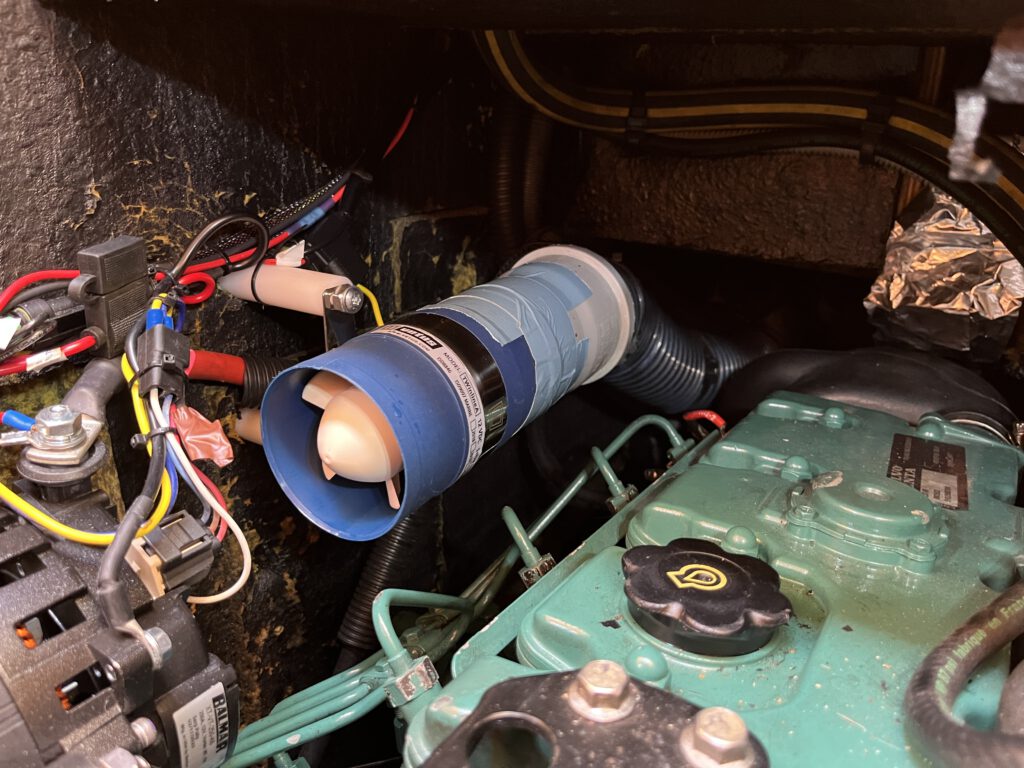
"🚀 Exploring New Horizons: Optimizing Boat Power Supply ⚡️ Stay Tuned for Updates! 🌊"
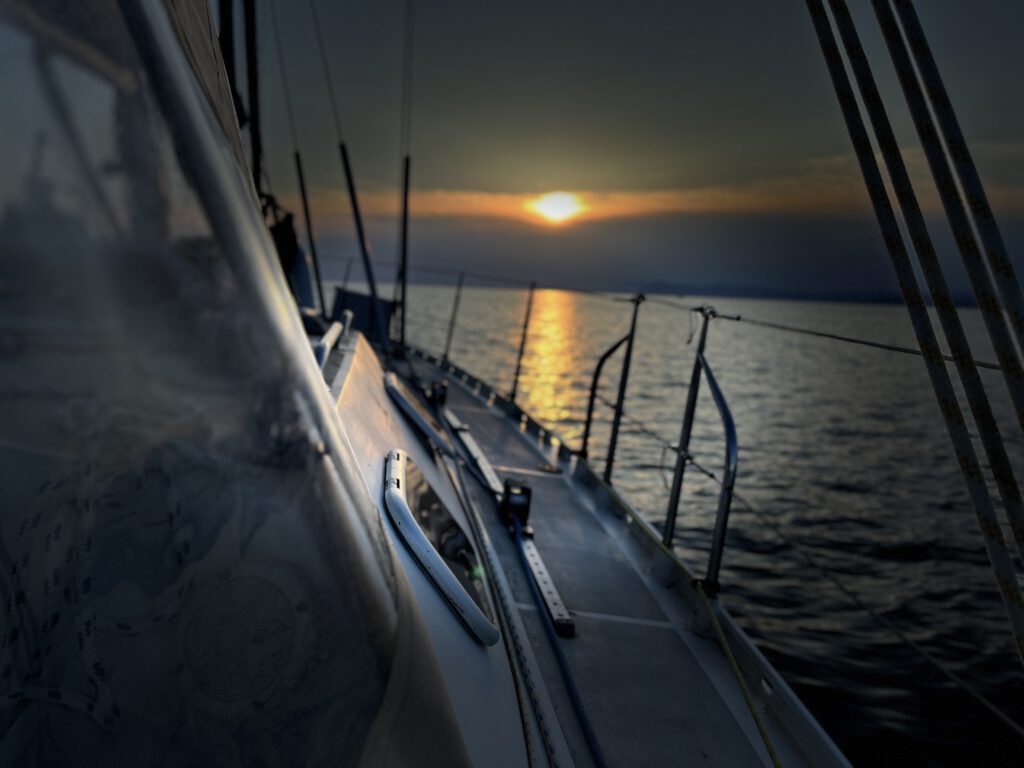
As I pondered my next move, two intriguing ideas emerged. Firstly, I plan to optimize the airflow in the outgoing pipe to ensure efficient heat dissipation. Secondly, I’ll explore the possibility of incorporating a heat exchanger into the system. With these potential solutions on the horizon, the quest for maximizing charging power continues. Stay tuned for updates on how I tackle this challenge and optimize my boat’s power supply system. To be continued…
If you followed me to the end of this blog , you may like these T-Shirts:
at Le Coeur Vert Boutique
Why don’t you use a water cooled alternator? Air cooled alternators are not compatible with sailboat engine rooms.
I have a similar size LiFePo battery bank, same engine on a Ovni 395. I am about to go down the path of alternator upgrade and was hoping you found the answer.
Looks like I will need to look into water cooled solutions. There are some available out there, but adapting them to the Volvo will be interesting.
Hi Thomas,
I’ve been down a similar path with my alternator, and I also tried cooling it down by increasing airflow inside the engine room. Unfortunately, it hasn’t been very effective, mainly because the air inside the engine room is already too hot. It seems like the key would be bringing in cooler air from outside, but that’s a bit tricky to set up.
Hi Maria,
Are you saying you were only blowing air that is already in the engine bay, over the alternator? So that is hot air being blown around. I would say getting fresh cool air from outside blown over the alternator would help. I also have a D2-55 and have these issues in front of me on my Garcia 42.
Hi Mark,
Yes, until now, I was only trying to extract the hot air from the engine compartment and vent it outside. My next attempt this spring will be, as you suggested, to blow fresh air from outside directly onto the alternator. Hopefully, that will improve cooling.