In this blog, I consider the following factors when choosing an alternator to charge LiFePO4 batteries on a boat:
Battery bank size: Determine the size of your battery bank and calculate the required charging power to ensure it can be charged within a certain timeframe.
Engine power
Speed ratio: Check the speed ratio between the alternator and the engine to ensure the alternator operates within its safe speed range.
Insulated ground: because it is on an aluminum boat.
Regulator: internal regulator (IR) or not
Compatibility: Ensure the alternator is compatible with electrical system voltage.
Constraints
The battery bank
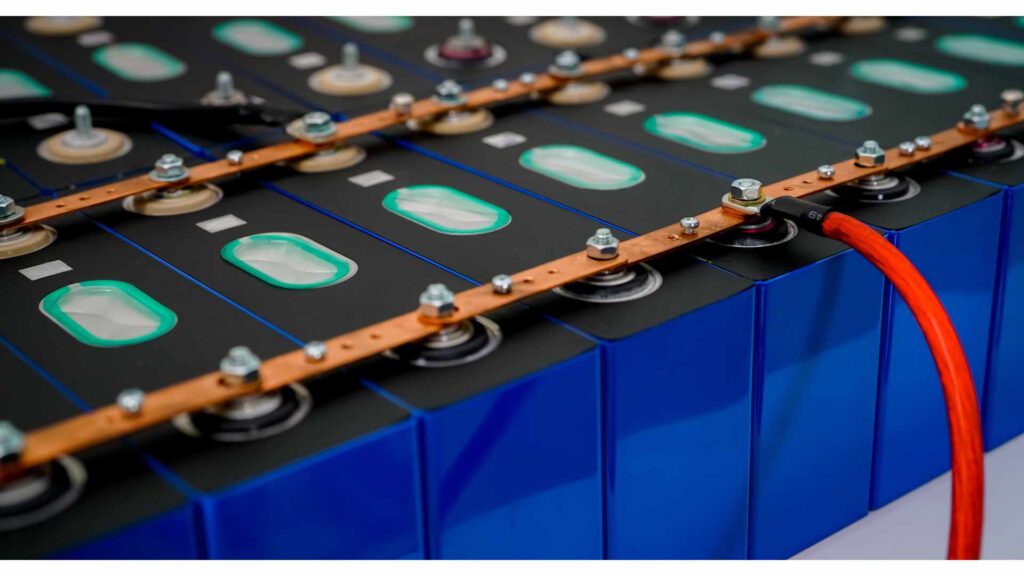
I will install 460AH x 2 with 12.8V, so 11.6kWh. In the event that the batteries are discharged, for example because I have prepared a large dinner with friends, I will have to keep the engine running to recharge the batteries. I also have a 330W solar, but I can neglect that in my calculations.
Plan is to be able to charge the batteries in a maximum of 4 hours with the engine running.
That means I need at least a 2.9kW alternator. The alternators used to run on 14V, so I need a constant min. 207A generator/alternator.
Aluminium boat
My boat is an aluminum Alubat Ovni with a Volvo Penta D2-55 diesel engine. To avoid aluminum corrosion (electrolysis) I can’t connect the ground to the boat hull. Most common alternators have the mass on the housing. This means I need to find an insulated ground (IG) alternator or isolate the alternator housing from the engine with an insulating bracket.
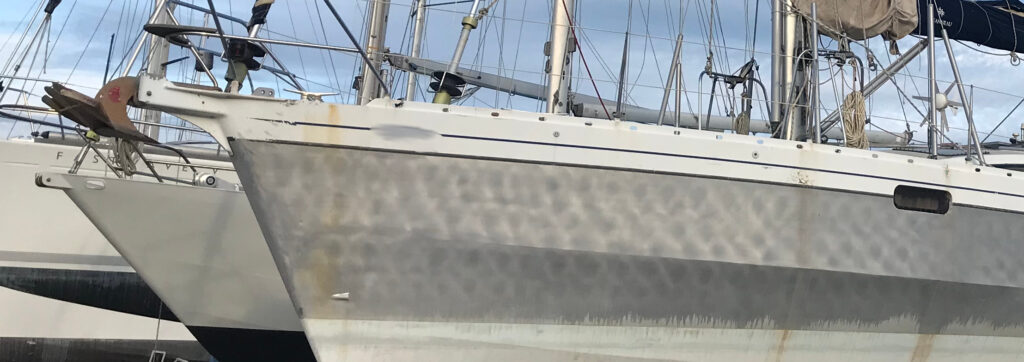
Regulator
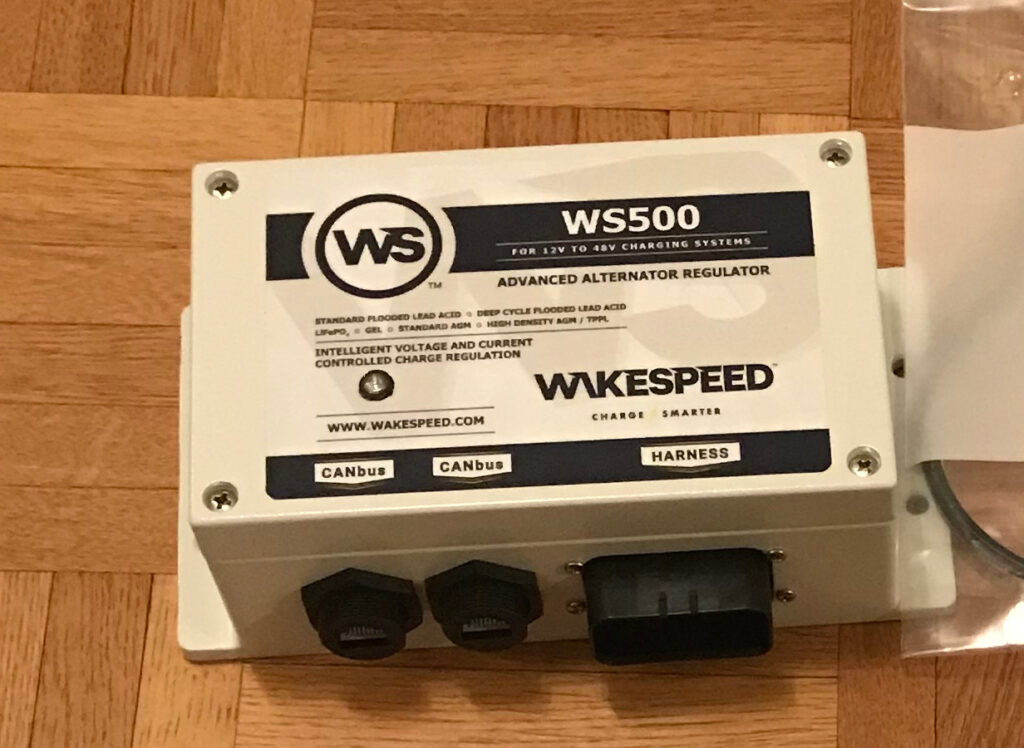
The Volvo Penta D2-55 diesel engine is not very powerful, so I also plan to regulate the alternator with a Wakespeed controller. (Described in previous post) This means I need an alternator with no internal regulator (no IR).
Speed ratio
Speed ratio between alternator and diesel engine will be 2.3 in my case. The maximum speed of the diesel engine is probably 4000 rpm without load. The maximum speed of the alternator is 9000 rpm. So I would be on safe operation even if the engine decides to go to top speed.
Which alternator or generator to use to charge the batteries?
Automotive alternators
There are many alternators on the market, especially from the automotive industry. I’ve been thinking about buying one. The electrical output characteristics of vehicle alternators are mostly as follows:
The power output starts at 1500 rpm alternator speed. So it doesn’t deliver any power when idling.
The 270A alternator delivers my desired 207A at an alternator speed of 5000 rpm, which corresponds to an engine speed of 2200 rpm in a cold environment (23 °C). It will never deliver the desired 207A in a warm environment. (max about 170A)
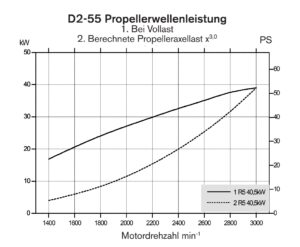
Actually, I would like to run the engine at about 1500 rpm for charging. At that speed (20kW) it has largely enough power for charging (3kW) and boat propulsion (6kW). At higher speeds it gets pretty loud in the boat.
The engine room is pretty small and warm so I’ll probably never get the 207A from this alternator. The solution is to choose a larger alternator, maybe 300A. On the one hand, the 300A alternators are much larger and more expensive.
A few more thoughts:
The automotive alternators are not designed to run at maximum load for long periods of time. In the car, they usually cover the power needs of the system and on rare occasions charge the 12V battery when it is empty after a long period of inactivity. No need to charge 11kWh batteries.
Electrical engines
In the automotive industry, when lithium-ion batteries over 1kW are implemented, the alternator is replaced by a 48V or high-voltage electric motor (belt starter generator (BSG), …). The electronics for these electric motors are usually water-cooled in order to be able to run for a long time under heavy loads.
I thought about implementing a BSG in the boat. Because my system runs on 12v and I don’t have the money to redesign everything is not possible. The voltage of the electric motors is at least 48 V. These motors are also more expensive than the alternators
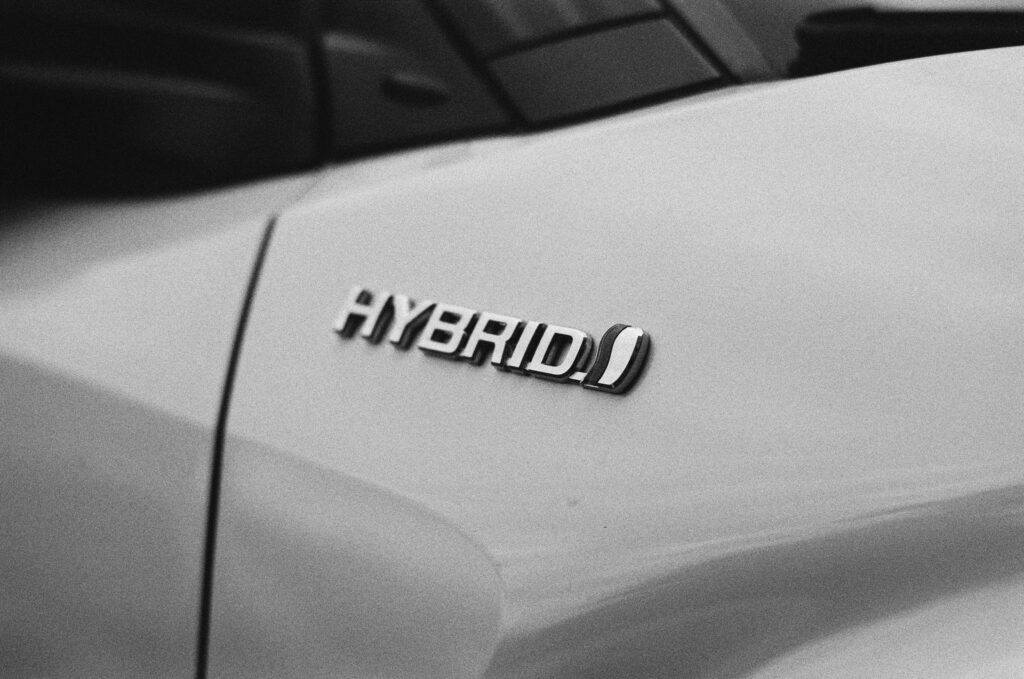
Best fit
Even in warm conditions it has 100 amps at idle speed. With normal charge at 1500 rpm engine speed (3450 rpm alternator speed) the power can be up to 270A in cold environment (25 degrees C) and 197A (in saturation). That looks pretty good!
This alternator is available without IR. Oddly enough, it’s more expensive without IR than with IR. I do not understand that. If I leave out a part, shouldn’t it be cheaper to produce? Let me know in the comments if you have any idea why the non-IR alternator is more expensive!
What's next?
The tricky part for me now is building my own drive belt system to fit on the engine as alternator number 2.
Also, I need to develop an insulated mount for this alternator on the engine.
I keep you updated!
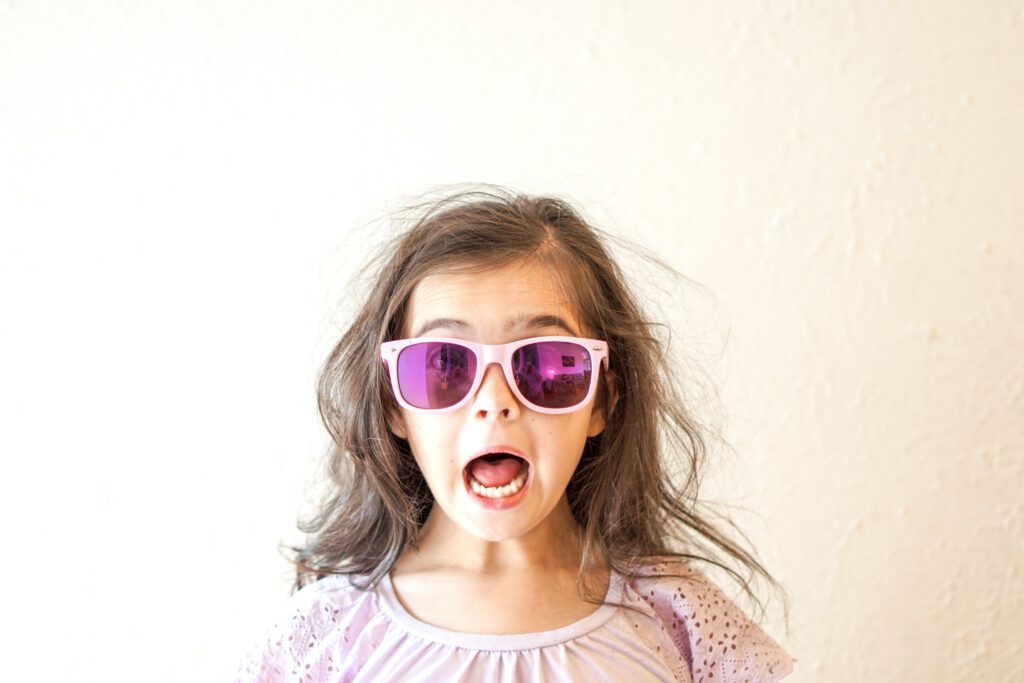
If you followed me to the end of this blog this is for you:
T-shirts for the tech enthusiasts and chemist among the readers
at Le Coeur Vert Boutique